Understanding CM/GC. Pt. 1 - Methodology
- Matthew Costabile
- Apr 18, 2023
- 2 min read
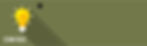
In 2023, local and state agencies continue to grapple with the dual challenges of aging infrastructure and population growth. In concert, the complexity and value of public works projects have sharply risen in response to increased regulation and market dynamics.
In this environment, traditional procurement methods like Design-Bid-Build are increasingly joined by innovative Alternative Project Delivery (APD) models, including Design-Build (DB), Progressive Design-Build (PDB), Public-Private Partnerships (P3), and Construction Manager/General Contractor (CM/GC).
One of the most widely adopted APD models is CM/GC. This article, part of Mission Critical's "Alternative Project Delivery 101" series, explores the key components of CM/GC, reviews the CM/GC procurement process, and summarizes the benefits of this innovative APD method.
What is CM/GC?
Construction Manager/General Contractor (CM/GC) project delivery integrates planning, design, and construction. In CM/GC, the project Owner selects the Contractor through a qualifications-based procurement process.
During the project's design or "preconstruction" phase, the contractor acts as the Construction Manager (CM). In this role, the contractor offers consulting and analysis, providing insights into the feasibility and pricing of different design options and identifying potential risks and solutions to constructability and delivery challenges.

As the design advances through the preconstruction phase, the Contractor provides the Owner and Designer with Opinion of Probable Construction Cost (OPCC) estimates at established milestones. OPCC estimates support the cost/benefit analysis of options and decisions and help the entire project delivery team assess the project's current cost vs. the projected budget or Engineer's Estimate. OPCC data and estimates are refined into a final, comprehensive cost to construct the project. Although quite rare, if the Owner and Contractor cannot agree on the final cost to build the project, the Owner may exercise the option to re-solicit the project using a traditional Design-Bid-Build method.
On acceptance of the final cost, the Owner issues a Notice to Proceed for the construction phase, and the Contractor then assumes the role of General Contractor (GC) and builds the project, using plans developed during the preconstruction phase that include the best means and methods for construction paired with solutions to manage and mitigate construction risks.
Critical Components of CM/GC
Early Collaboration and Integration
As mentioned above, CM/GC involves the Contractor from the early stages of the preliminary design. During preconstruction, the Contractor, Owner, and Designer work together to advance design from an initial step, typically 20% - 30% design completion.
Early integration aligns Owner, project, and stakeholder goals and drives an early understanding of the project scope, schedule, and potential challenges across the project delivery team. This collaboration also enables the Owner to actively participate in the design process and make educated decisions utilizing the Contractor's specialized expertise.
Constructability Reviews and Iterative Cost Estimation
One of the main functions of the Contractor during preconstruction is to provide insights into constructability, risk, cost, and scheduling. These insights come from the Contractor's experience and lessons learned on similar work, including construction methods, materials, and local regulations. The Contractor provides constructability input, analysis, and current cost and market data throughout the design. Integrating real-time cost information, construction expertise, and design control enables the team to make informed choices quickly, adapting to changes or resolving issues promptly.
Risk Identification, Management, and Mitigation
The CM/GC method emphasizes risk identification and mitigation during preconstruction. The team uses a risk register to document and analyze potential risks, evaluating their probability and potential impact on construction. The joint Owner-Designer-Contractor team then decides on the best way to manage or eliminate these risks or allocate contingencies for variable risks (e.g., the cost to remediate unknown quantities of unsuitable soil). CM/GC provides the framework to mitigate uncertainty and reduce potential cost overruns.
Value Engineering and Innovation
The CM/GC method encourages value engineering and innovation through a transparent and iterative design process. The Contractor's early involvement enables them to suggest alternative materials, construction techniques, or design modifications that can enhance value without compromising quality. This approach often leads to creative solutions that address complex challenges, improving functionality and reducing costs.
Owner Design Control
Unlike Design-Build (DB) or Progressive Design-Build (PDB) projects, where the Designer is part of the Contractor's delivery team, CM/GC allows the Owner to maintain direct control over the design. This control empowers the Owner to guide decisions during preconstruction to meet their specific needs and preferences. Simultaneously, the Contractor's input ensures the design is practical and cost-effective, thus integrating the Owner's vision with construction realities.
Shared Responsibility and Joint Actions
The integrated approach of CM/GC promotes open communication and relationship building among all parties. Regular meetings, joint problem-solving sessions, and shared responsibility for project success foster trust and teamwork. This enhanced collaboration can lead to a smoother construction phase as the relationships and understanding developed during preconstruction are carried forward and continue throughout construction.
Overlapping Design and Construction
The Contractor's collaborative environment and early engagement often allow for overlapping design and construction using early work packages to advance scope items that pose risks to the project's critical path. These packages may include long-lead material procurements, completion of early structures work to facilitate high-volume pavement scope, environmental mitigations, and early utility identification and relocation.
CM/GC emphasizes integration during the preconstruction phase and sets the stage for a more cohesive and efficient project lifecycle. By fostering collaboration, enhancing communication, encouraging innovation, and enabling real-time decision-making, CM/GC streamlines the transition from design to construction.
Using the Contractor's knowledge and expertise, this integrated approach can significantly reduce risks and costs for complex or technically challenging projects while meeting the Owner's goals with precision and creativity.
Up Next: Part 2 - CM/GC - "The Process".
Learn More
If you found this article interesting, join our mailing list below to be notified of the next article in the series: "New to CM/GC? Competitive Strategies to Explore Now." (October 2023)
Explore the first article in Mission Critical's "Alternative Project Delivery 101" series: APD 101 - What is Alternative Project Delivery?
Learn about Mission Critical's latest CM/GC win – $95M SM-82 El Camino Real Roadway Rehabilitation